Share
In manufacturing, there has been no shortage of disruption. Fundamental changes are shaking up the way products are designed and made. Volatile supply chains. Complex and distributed teams. Geopolitical unrest. Inflation. These challenges are faced at the same time we see an unprecedented pace of technology change: ever-lower compute costs, accelerating cloud adoption, and the practical application of AI to make our systems smarter.
But disruption means opportunity. That’s why I’m excited to be leading Product Development and Manufacturing Solutions at Autodesk at this transformational time.
I’ve always been drawn to industries in transformation, and have helped lead digital transformations in travel, financial services, small business, and enterprise software. Given the reach and impact of manufacturing, our industry is undergoing an especially compelling transformation. Manufacturers have long embraced technology, but margins are tight and switching costs are high. Waiting on expensive new technology to incrementally improve processes isn’t sensible in today’s fast-paced environment. The industry is ripe for disruption by solutions that deliver great outcomes affordably.
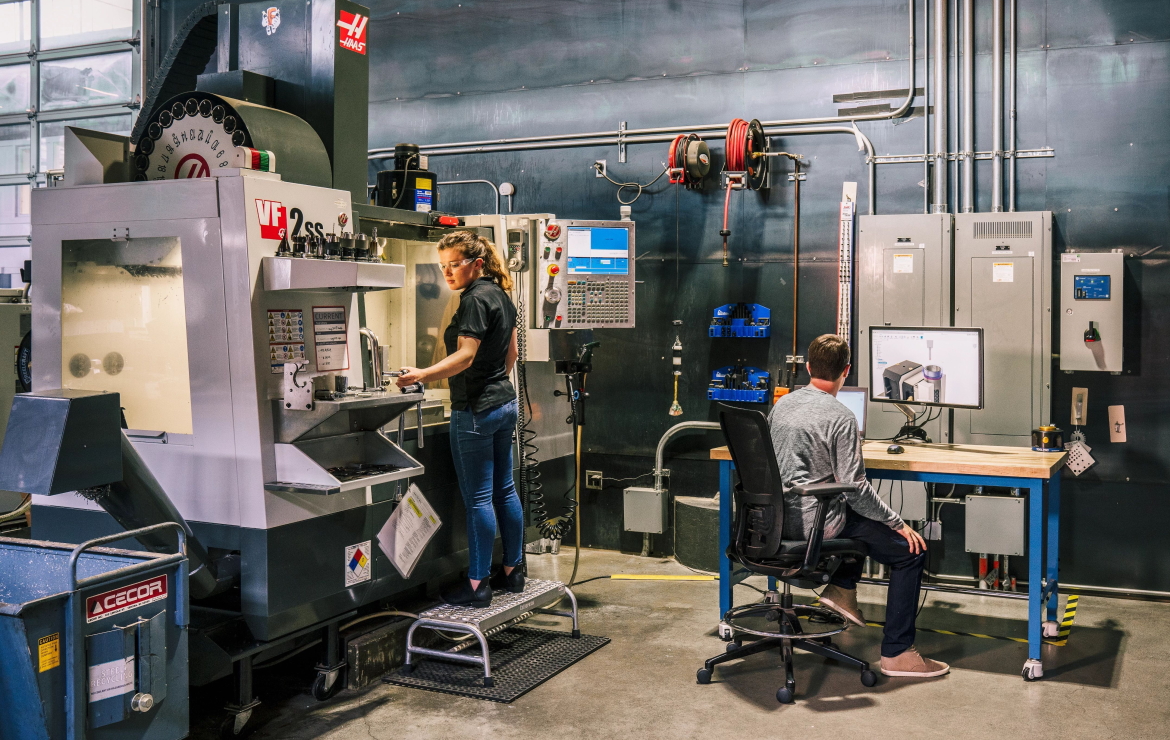
Employees use Autodesk Fusion 360, a cloud platform that powers digital transformation, at the Autodesk San Francisco Technology Center.
The good news is Autodesk began preparing for this transformation long ago. Autodesk has been a pioneer in computer-aided design (CAD)—and kept going by joining forces with pioneers in computer-aided manufacturing (CAM). We were early champions of cloud computing, convinced that it would be the future. We also believed unlocking data would accelerate the pace of automation. We saw the need for a single environment for design and make workflows where data moves easily and teams collaborate naturally across machines, systems, locations, and time zones. We also observed software use habits change and were one of the first in our industry to offer subscriptions as well as flexible, pay-as-you-go pricing—so what you pay aligns with the value you get from our software.
This foresight and subsequent investments led to Autodesk Fusion 360—a cloud platform that powers digital transformation and connects the entire product lifecycle. With Fusion, you no longer live in a land of exchanging massive, outdated project files. Gone are the days of closed manufacturing systems that are expensive to deploy. The new standard for manufacturing is a connected system where data flows seamlessly from concept to design, from plan to manufacture—even to testing and procurement.
I’m confident that with Fusion, we will help our customers win today and win ten years from now.
An accelerating innovation journey
The pandemic accelerated the trends Autodesk has invested in for years. Remote work became a reality overnight. Manufacturers needed new ways to collaborate and turned to Autodesk, the leader in bringing together teams across disciplines, industries, and regions through the cloud. And we delivered. Manufacturers saw they could manage design changes at any stage of production. Automate repetitive tasks. Reduce waste. And get to market faster with better products—despite being remote.
Autodesk already had a lead in this journey, and now we’re extending it.
Our ambitions are centered around the convergence of design, manufacturing, and the many other functions involved in producing a product. We’re unifying enterprise-grade technologies—CAD, CAM, PCB design, CAE, PDM, PLM, MES, and more—so you have a single, end-to-end platform that everyone works on together. This will be the platform for creating a complete digital representation of your product, how it’s made, its components and supply chain, and even collecting data from the product to create a digital twin that will improve future designs. Key to this is data moving fluidly throughout the organization and across your external ecosystem of suppliers, contractors, and customers.
Through generative design, engineers can design from the outside in, starting with requirements and ending with hundreds of pre-validated options. With generative design and additive manufacturing, products that once required dozens of parts to produce can be engineered as one piece. Through simulation, designers can endlessly ask “what if” without costly, wasteful prototypes.
The outcomes are striking. Take our United Kingdom-based customer, Brown & Holmes, for example. The company specializes in workholding solutions, precision machining, and products including robots and high-pressure vices. When an uptick in orders led the company to upgrade to the Autodesk Product Design and Manufacturing Collection and Fusion, they were able to give CAM capabilities to operators on the shop floor. The company eliminated the bottleneck of CNC operators waiting for office-based programmers to create code for multiple machines.
As a result of its investment in Fusion and the machining extension, Brown & Holmes increased manufacturing throughput, reduced non-conformance by 34%, and doubled its revenue.
More to come at Autodesk University
This is just scratching the surface of the opportunities that lie ahead in manufacturing. By connecting people and processes with technology, I believe we will transform the industry for the better. We will accelerate productivity and build smarter, better, more sustainable products faster—while workers will have more time to focus on new skills that tap creativity and human ingenuity.
I look forward to sharing more with you about unlocking innovation through digital transformation at Autodesk University.
I hope to see you there – in-person or online!