Share
In the past few weeks, many major manufacturers have shuttered production as global economies come to a halt due to the coronavirus. As healthcare systems operate past capacity to contain the crisis, the disruption in the manufacturing supply chain has added to the stress by creating a global shortage in personal protective equipment (PPE).
The Autodesk Technology Centers were designed as spaces for exploring new possibilities for making, so in an effort to support healthcare workers on the frontlines, the teams at the centers are taking action.
Utilizing the resources available at Autodesk workshops in San Francisco, Boston, Toronto, and Birmingham, UK, technology center members have joined forces to help bridge the gap in PPE shortages by facilitating production of much-needed face shields.
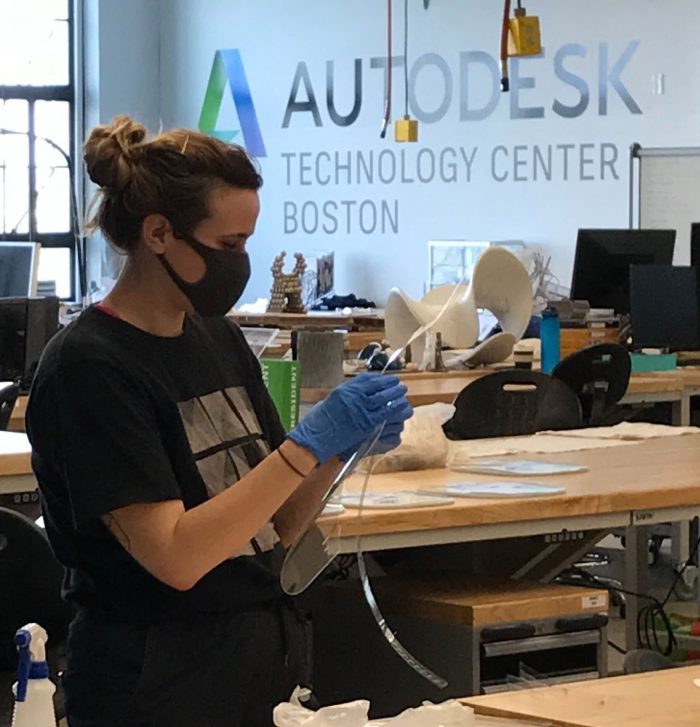
An Autodesk employee constructs a face shield at the Technology Center in Boston.
In Boston, employee volunteers led by technology center shop staff are using an open-source design to produce a single fold origami-style face shield, laser cut from polyethylene terephthalate (PET), plus a small headband cut from the same material. Nearly 5,000 face shields have been donated across 13 medical clinics in the state. “The feedback I have received from the organizations has been positive. Hearing how useful our face shields have been truly makes me proud to be a part of this project,” said Joe Aronis, a workshop manager in Boston.
“It was very therapeutic to do something physical with my hands and see the stack of ready–to–ship masks grow and the boxes fill up,” said volunteer Lilli Smith, a senior project manager at Autodesk.
Learn more about PPE production efforts.
At the technology center in Birmingham, the same open–source design is being used to produce origami–style face shields with a modification using Velcro. To date, approximately 1,800 face shields have been delivered to the National Health Service, with more in production.
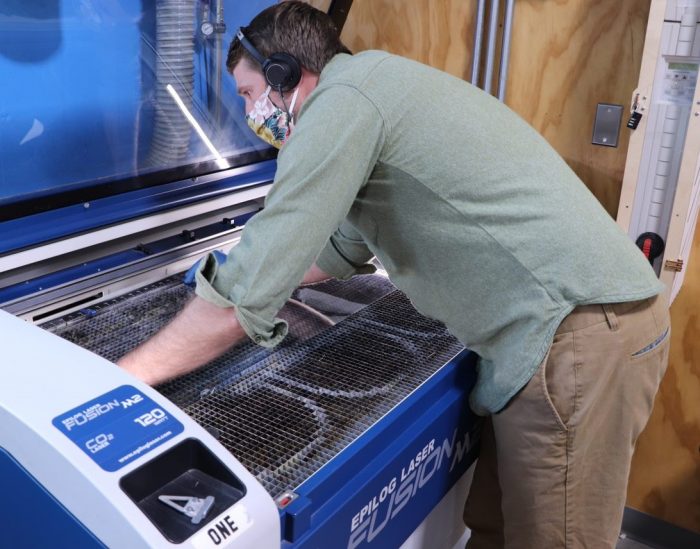
A workshop member at the Boston Technology Center uses a laser cutter to cut PET material for face shields.
In Toronto, the technology center loaned three Markforged 3D printers to the resident team at Advanced Perioperative Imaging Lab (APIL) to produce their version of an open-source visor-style face shield created by medical hardware maker Glia as part of a project with Toronto General Hospital (TGH). They are currently producing between 150-200 face shields per day for medical staff at TGH and other hospitals across the country and hope to ramp up production with the additional printer resources.
“One thing we’ve been learning quickly, and rather painfully, is how to manage these distributed manufacturing models,” said Dr. Azad Mashari, chief anesthesiologist and director at APIL. “It’s fairly tractable when you have one organization volunteering 40 printers or when you have a few large pods like that… it gets much more complex when many people want to commit… we don’t yet have a sustainable model for managing a large network of small producers in a system of distributed manufacturing.”
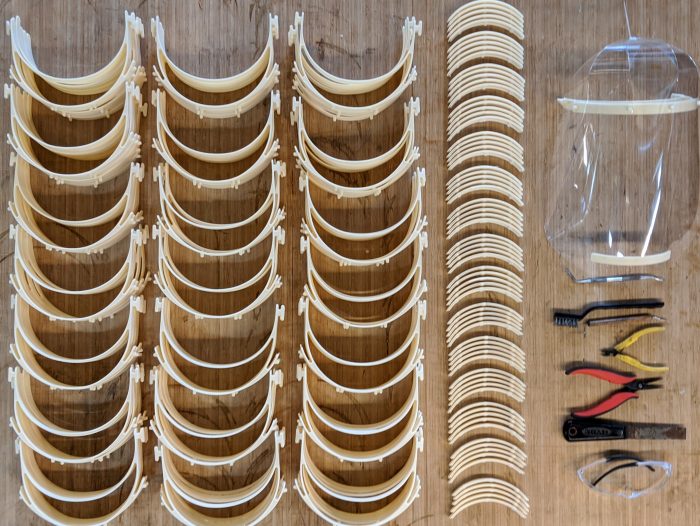
A selection of face shields produced at the Autodesk Technology Center in San Francisco, CA.
In San Francisco, the workshop team is 3D–printing parts for face shields by Maker Nexus, a non-profit makerspace community, who organized the efforts and designed the PPE for easy production. “Autodesk has been instrumental in supporting the efforts underway at Maker Nexus, and other makerspaces across the country, to rapidly produce critically needed personal protective equipment for our frontline medical professionals,” said Eric Hess, general manager at Maker Nexus.
On site at the technology center workshop, the team is printing in ABS and ASA on the Stratysys Fortus machines, while offsite, they are printing with polyester on the Ultimaker. More than 560 face shields will be donated to Bay Area medical facilities.
In the months of March and April, the technology centers have produced and donated more than 7,000 units of PPE to over a dozen healthcare facilities, with the capacity to produce a few thousand more.
For most major manufacturers and automated factories in North America, pivoting to develop PPE is not an easy switch. There are many factors to consider before changing gears and retooling to be able to produce these items in high volumes. Sunny Sahota, a technology center engagement manager in San Francisco, noted, “At a high level, the cost of change for larger manufacturers is quite high, both financially and on labor. A lot of it comes down to a company’s ability to prioritize agility in manufacturing.”
For the technology centers, producing PPE has been possible due to our agile and adaptable environment, while navigating such challenges as office closures, complying to social distancing protocols and sourcing materials.
“We will continue to make face shields to support the need until industry supply chains tool up or we run out of material,” said Aronis. “At that point, we will see if there are other needs that we could support at the technology centers.”
Learn more about the Autodesk Technology Center efforts.