Share
Mention smart manufacturing to most people and a number of different concepts will come to mind depending on who you’re talking to. Take Industry 4.0. The high-tech strategy of the German government promotes the computerisation of traditional industries such as manufacturing. Its goal is the intelligent or smart factory, a unit that benefits from adaptability, resource efficiency and ergonomics, as well as the integration of customers and business partners in business and value processes.
Others will think of China 4IR. The Made in China 2025 strategy aims to turn China into a global manufacturing power able to influence global standards and supply chains, and to drive global innovation.
In the United States, the Smart Manufacturing Leadership Coalition, is a non-profit organisation comprising practitioners, suppliers and technology companies plus universities and government agencies. Here the aim is to enable stakeholders in the manufacturing industry to enable collaborative research and development, standards and shared infrastructure that facilitate the adoption of manufacturing intelligence.
The approaches might be many and varied but, according to Callan Carpenter, vice president of digital manufacturing and named accounts at Autodesk, a leading producer of software for manufacturers, the central idea is simple. “Don’t worry about the jargon and buzzwords,” he explains. “Smart manufacturing is about exploring more solutions and building better products. At Autodesk we believe that smart manufacturing is simply about doing more, doing it better, with less negative impact on the planet.”
Businesses, often overwhelmed by change, can make small, incremental investments focused on key areas, says Mr Carpenter. “Data is the lifeblood, the new oil of the digital business, but the key is to capture the right data so you have enough compute power to analyse and interrogate it to draw essential insights.”
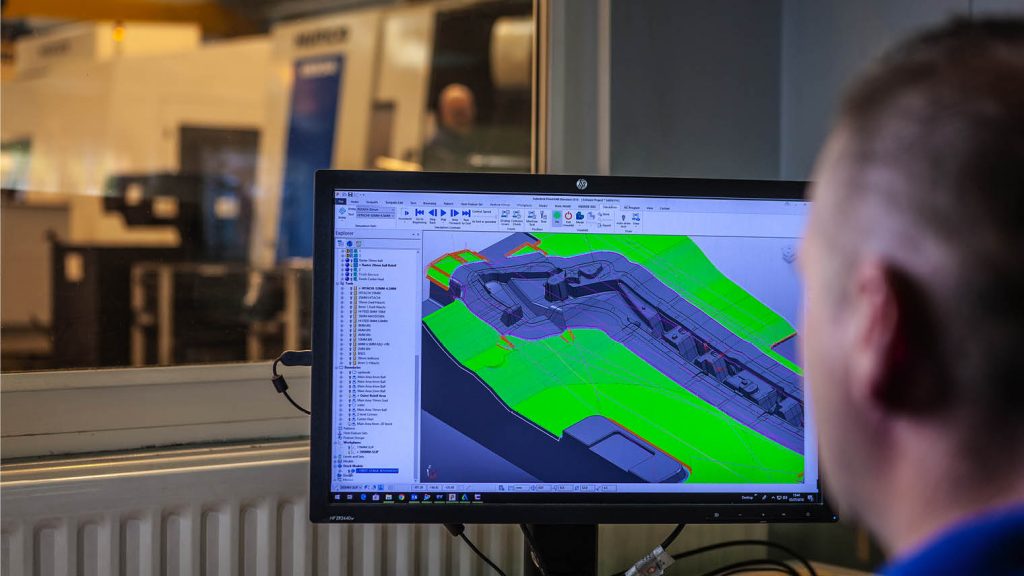
Autodesk PowerMill automates complex manufacturing operations
The revolution currently taking place in the manufacturing industry is throwing up challenges for many, but those ready to embrace smart manufacturing are already benefiting from the opportunities it offers. Products need to come to market faster than ever and their shelf life is now shorter, offering agile companies the chance to steal a march on the competition.
Near-shoring means items are being produced nearer their intended customers rather than a month away by container ship so small runs can be ordered on a just-in-time delivery basis. “Customers expect to get their items more quickly, but they also want what they buy to be customised to them as an individual,” says Mr Carpenter. “This might be shoes that are designed to fit your feet exactly or cars which offer you millions of options. A major automotive customer recently mentioned to us that even with a production run of 300,000 there are so many variants that no two are identical.”
Meanwhile, customers are also demanding the kind of improved product performance that can only be achieved with advanced materials and processes. Twenty years ago, carbon fibre was only to be found in aerospace. A decade later it had reached the highest performance street cars. Today, thanks to customer expectations of cars that are faster, safer and more fuel efficient, it’s increasingly common across the entire industry.
However, smart manufacturing can help businesses meet these challenges and make the most of the opportunities. Increased automation is not only increasing efficiency, but it’s taking away manual, repetitive or low-skilled jobs like manual setups, simple tool paths, manual finishing from machine operators, and automating them to boost productivity.
Smart manufacturing is about exploring more solutions and building better products. At Autodesk we believe that smart manufacturing is simply about doing more, doing it better, with less negative impact on the planet
Alongside this change, connected manufacturing is making communications between machine and departments easier. Typical reporting, logging, inventory tracking and times are being cut so skilled workers can utilise their time better to deliver quality products on schedule.
Steve Hobbs, vice president of computer-aided and hybrid manufacturing at Autodesk, says: “We’re finding that manufacturers are coming to us for help because their manufacturing process is increasingly collaborative and they need technology that connects more and more people to increasingly complex projects. We’re going to see global virtual teams and collaboration on a scale unheard of so that’s why we introduced Shared Views and Autodesk Drive into our manufacturing technologies such as PowerMill.”
Shared Views enables manufacturers to share engineering data with key stakeholders, anywhere, anytime with cloud-connected devices, to request approval or to provide easy access to a field sales team for on-site presentations.
Greater integration of the digital and physical means digital systems are becoming deeply integrated into physical things, creating complex inter-relationships among physical objects. Ubiquitous and inexpensive sensors connected to production hubs mean places, things and media will be connected, intelligent and dynamic.
“Products can now gather and stream data about how they’re being used to provide valuable insights about the needs of the end-customer for the next iteration of the product,” says Mr Hobbs. “As a result, that product can come to market more quickly and it’s more likely to be what customers are asking for. We find that when companies experience the practical benefits like this, things they can actually get their arms around, then they really start to embrace the future of making things.”
This article originally appeared on The Times of London’s Raconteur website as part of a special report on the Future of Manufacturing.