Share
As manufacturing becomes increasingly complex, more efficient engineering workflows are required to ensure timely deployment of critical manufacturing assets on the factory floor. To address this need, Autodesk and Rockwell Automation are working together to streamline data flow between their respective solutions to enable customers to more effectively, design, lay out and virtually commission factory systems for better optimization and less risk.
Autodesk offers powerful 2D and 3D digital factory layout tools as part of our Product Design & Manufacturing Collection, while Rockwell Automation brings its sophisticated simulation capabilities in Emulate3D to help demonstrate, simulate and virtually commission manufacturing assets. Synched together with smooth data flow, these solutions allow companies to digitally design and commission factories in less time, with greater efficiency.
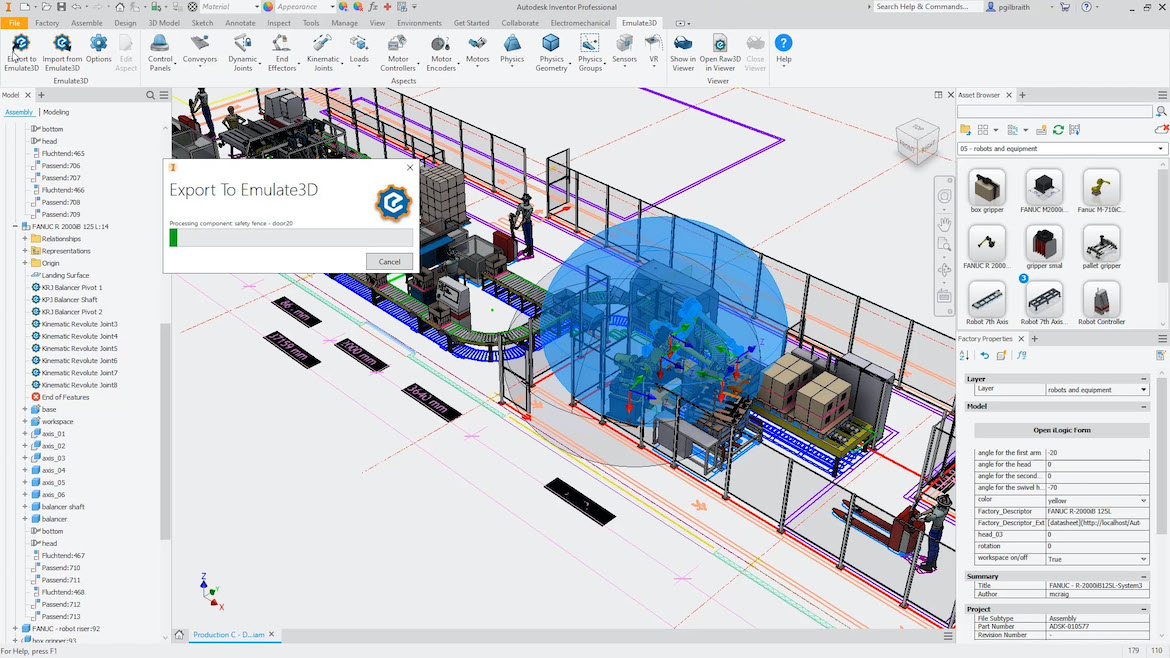
Autodesk Product Design & Manufacturing Collection customers now have the ability to add operational and functional parameters of a machine during the factory design phase.
Virtual commissioning has become a vital tool for organizations to quickly get a physical manufacturing environment up and running. It involves creating a digital twin from a 3D CAD model, linking automation systems and connecting models, making it possible to virtually demonstrate, simulate, and optimize the performance of an entire manufacturing operation.
“Bringing together the specialized expertise of Autodesk and Rockwell means we can better address needs throughout the factory lifecycle, from design through virtual commissioning, operations and maintenance,” said Derrek Cooper, vice president of product development & manufacturing solutions, Autodesk. “This is a crucial step in the creation of digital twins and will give our customers the ability to get more out of their data, extending design models to help optimize operations and connect across the growing digital ecosystem.”
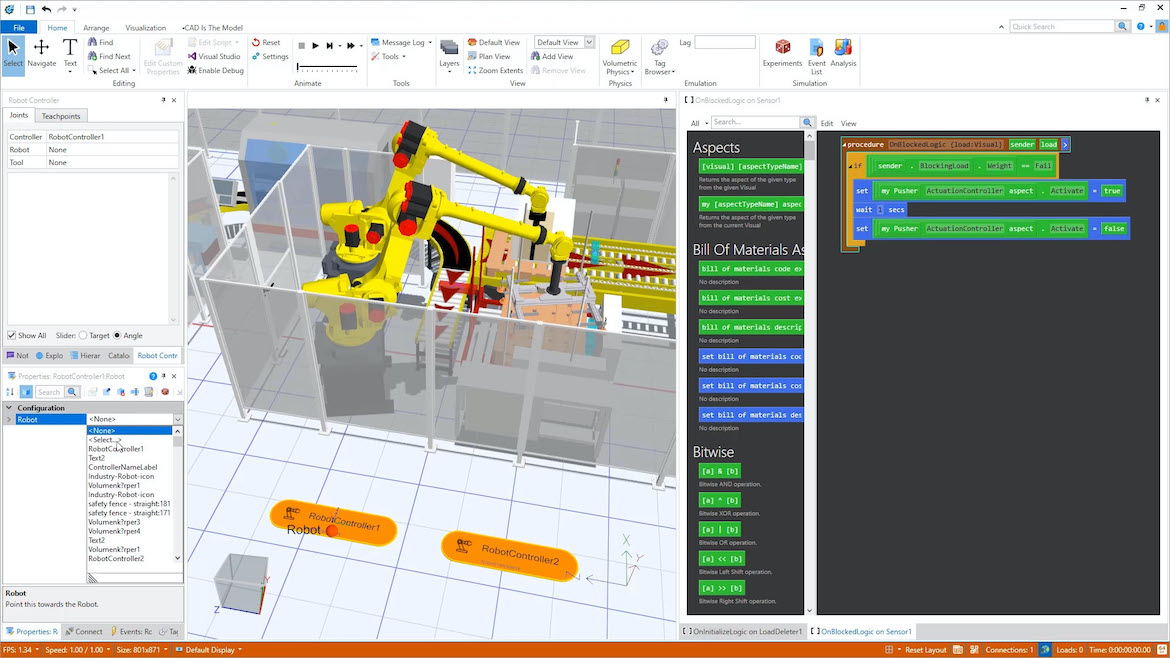
Virtual commissioning with a digital twin allows you to configure, test and simulate systems before they are built.
The ability to add operational and functional parameters to manufacturing assets during the design phase opens new opportunities for customers to further hone increasingly complex workflows.
“Enabling commissioning of manufacturing assets in a virtual environment helps separate it from the critical path,” said John Pritchard, digital engineering business lead, Rockwell Automation. “It’s now possible to optimize the integration of hardware, software and controls early in the factory layout process, reducing project risk as manufacturers look to expand.”