General Motors’ auto engineers have been heavyweights in vehicle lightweighting for years. Just since 2016, GM has launched 14 new vehicle models with a total mass reduction of over 5000 pounds or more than 350 pounds per vehicle. The lighter the car, the less fuel it uses, the less carbon it emits and the more money the driver saves. Pretty important stuff.
Now to push the boundaries on its next generation of lightweighting, the automaker is teaming up with Autodesk to use a combination of generative design and additive manufacturing as key technologies to develop future cars and trucks, including its alternative propulsion and zero emission vehicles. As GM announced today, it is becoming the first major automaker in North America to adopt Autodesk generative design software to go beyond the weight reduction possible through traditional design optimization techniques.
Generative design is a design exploration technology that uses AI-based algorithms to simultaneously generate multiple valid solutions based on real-word manufacturing constraints and product performance requirements, such as strength, weight, materials and more. Engineers can explore and choose from far more manufacturing-ready design options, far more rapidly than was ever conceivable before. They are freed from repetitive design tasks so they can focus on higher-value decisions like maximizing part performance.
“This disruptive technology provides tremendous advancements in how we can design and develop components for our future vehicles to make them lighter and more efficient, said GM Vice President Ken Kelzer, Global Vehicle Components and Subsystems. “When we pair the design technology with manufacturing advancements such as 3D printing, our approach to vehicle development is completely transformed and is fundamentally different to co-create with the computer in ways we simply couldn’t have imagined before.”
In an initial proof-of-concept project, GM and Autodesk engineers working together at GM’s Tech Center in Warren, Michigan used generative design to reconceive a small, but important vehicle component – the seat bracket where seat belts are fastened. The software produced more than 150 valid design options based on parameters the engineers set, such as required connection points, strength and mass. They zeroed in on a new design, whose organic structure no human could have conceived on their own. It is 40 percent lighter and 20 percent stronger than the original part.
It also demonstrates another major benefit of generative design – part consolidation. The new part consolidates eight different components into one 3D-printed part.
Speaking of 3D printing, GM has been a leader in additive manufacturing for 30+ years and boasts one of the most comprehensive 3D printing arsenals in the auto industry. GM runs more than 50 rapid prototype machines that have produced more than 250,000 prototype parts over the last 10 years.
“With our long-standing expertise in additive manufacturing, we see incredible opportunities for generative design. The seat-bracket is just a small demonstration of the potential mass and strength improvements when we apply these technologies to many of the 30,000+ parts in our vehicles. Maybe even more exciting are the far-reaching transformations we can imagine as we move into an era of electric and autonomous vehicles,” commented Kevin Quinn, GM Director of Additive Manufacturing.
This seat bracket project is just the beginning of multi-year, innovation-focused alliance for GM and Autodesk. The two companies will collaborate on additional projects involving generative design, additive manufacturing and materials science. Executives and engineers will participate in a series of onsite engagements to exchange ideas, learnings, and expertise. In March, for example, two GM engineers participated in a two-week generative design residency at Autodesk’s Pier 9 technology center.
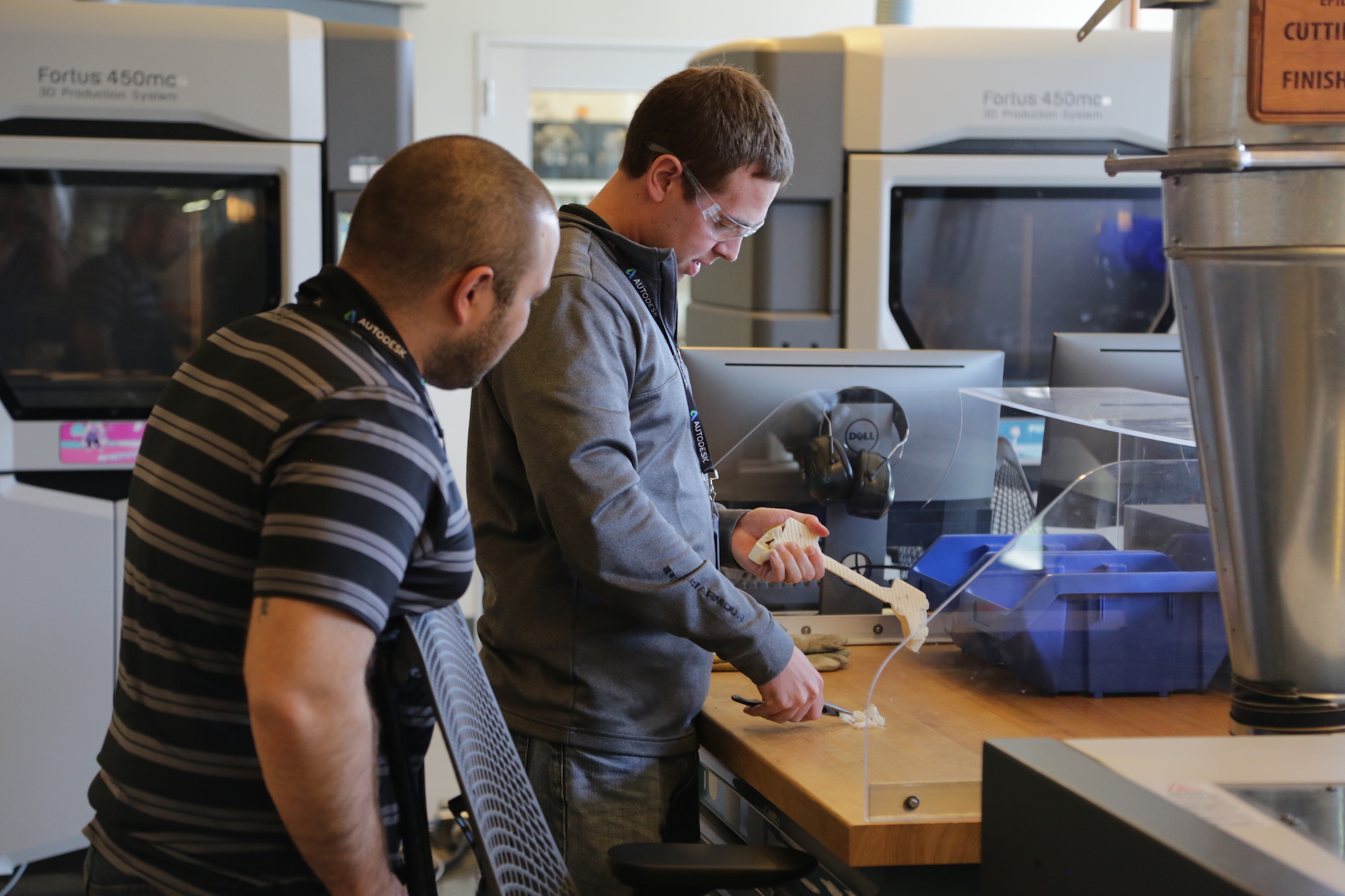
GM engineers Mike Van De Velde and Paul Wolcott at Autodesk’s Pier 9 additive manufacturing lab in San Francisco.
GM also has on-demand access to Autodesk technical specialists and its full portfolio of software. GM is already using Autodesk Fusion 360* for access to the generative design technology; Netfabb for lattice optimization and metal additive simulation, which helps prevent problems like heat distortion, shrinkage and crack propagation during 3D printing; as well as Alias, Recap Pro and Meshmixer.
“Generative design is the future of manufacturing, and GM is a pioneer in using it to lightweight their future vehicles,” said Scott Reese, Autodesk Senior Vice President for Manufacturing and Construction Products. “But the benefits for GM go well beyond lightweighting. What really separates generative design from past technologies is the ability to consolidate many parts into one and the ability to dramatically compress the product development process. Engineers get hundreds of ready-to-manufacture design options they could never come up with manually and it happens in a fraction of the time it would take to validate a single design the old way. GM can take advantage of those benefits right now for parts like the seat-bracket, and they are already looking to the longer-term potential to transform the consumer experience for their vehicles. ”
GM envisions a future where reducing vehicle weight and material not only saves gas and driver money, but can also extend electric car range and open up more interior space for passengers to enjoy. As GM notes in its press release, these new technologies can provide “vehicle designers a canvas on which to explore designs and shapes not seen today.”
“GM has an incredible history of innovation. Through our collaboration, we’re tapping into GM’s heritage and bringing new technologies into the mix to further invigorate that culture of innovation,” said Mike Grau, an Autodesk engineer who is working with the automotive engineering team in Warren, MI. “GM is taking a bold leap into the future. I can’t wait to see the incredible advances to their vehicles that is going to come out of our alliance.”
* Fusion 360 includes commercial availability of Autodesk’s generative design technology. Read the Sept. 6 blog post here.